Finding the Right Embedded Computing Framework for Railway Track Inspection
April 26, 2024
Story
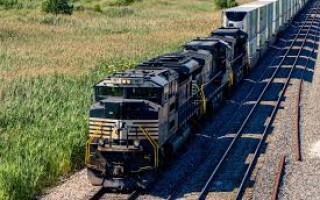
Norfolk Southern, a leading company in railway shipping, development, and maintenance was looking for a solution for a track inspection system. The company wanted to find a semi-rugged, reliable, and proven embedded computing architecture that was also cost-effective. As the design did not require particularly high speeds, the backplane architecture options were wide open.
The Application
Norfolk Southern required a computing system to inspect the track as their freight trains travel from site to site. There is a sensor box that is placed on the bottom of the train that measures the geometries of the track, down to 1mm of accuracy. Using lasers, gyroscopes, and accelerometers, the sensor gathers the data and sends it to the embedded computer for processing. It also sends data to a remote track inspection office for analysis.
Norfolk Southern needed an enclosure system that was a combination of semi-rugged, reliable, had redundant power options, and was a cost-effective solution. As the backplane speeds were not high, the VME architecture was a natural choice with its proven legacy in ruggedized systems. It’s also a lower-cost technology than higher speed open architectures such as OpenVPX. Mechanically, the Eurocard form factor that VME is based upon provided a ubiquitous framework, with plenty of space and I/O for their required signaling in the 6U board size. To remain cost-effective, the design engineers would need to try to find a standard solution that could be easily tailored to their specific requirement.
Fulfilling the Design Challenge
The Pixus 4U tall horizontal-mount VME chassis was an excellent fit for Norfolk Southern. (see Figure 1 and 2). The chassis has a semi-rugged design to meet the shock and vibration from the train. With a horizontal mount configuration using side-to-side airflow, the enclosure has a lower profile, taking up less rack height. It features an N+1 power solution with redundant pluggable power supply units on the front of the enclosure. Utilizing a 7-slot VME64x backplane, the chassis platform can send real-time data on track conditions. This helps the Norfolk Southern team in the inspection office make any repairs or adjustment that will improve the safety and efficiency of the track. This type of modular enclosure easily facilitates required customization such as incorporating SATA drives for memory/logging in the system.
Another customization requirement was to provide both AC and DC versions of the enclosure. The modular method facilitates a long legacy of standard approaches for both power types. The railway engineers use the DC powered solution for the freight trains. The AC powered design is utilized for smaller service and utility trucks that can ride on the tracks.
To ensure proper cooling of the system, the enclosure employs a redundant fan system in a push-pull configuration. The side-to-side airflow path efficiently cools the 6U VME boards in the enclosure. There are terminal blocks on the rear of the DC enclosure for power input into the system.
Figure 1 and 2 (Front and rear images of the enclosure)
Utilizing a modular and cost-effective chassis platform, Norfolk Southern was able to employ an embedded computing solution that met sizing, costing, I/O, storage, and signal processing requirements.
For more information, visit www.pixustechnologies.com