Achieving Mass Manufacturability for AR Smart Glasses
March 27, 2024
Sponsored Story
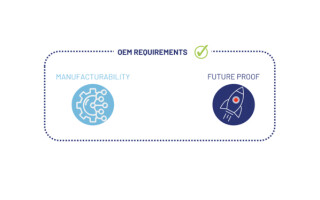
Augmented reality (AR) has been the subject of intense interest from science fiction writers and inventors for centuries, with the first actual prototypes appearing in the 1940s, but really taking off in the 1960s in military applications such as Head-Up Displays (HUD) and Head-Mounted Displays (HMD).
Augmented reality glasses have been manufactured in some form or another for many years, however, mass consumer adoption has not eventuated yet. Why is that? It’s not through lack of effort or investment, companies like Apple, Meta, and many others have invested millions on this journey.
It appears that the overriding issue is that the products to date have been evidently bulky, awkward, and unable to meet consumer expectations at an acceptable price point. AR glasses must feel comfortable, provide an excellent display, and be acceptable to other people around the wearer.
Product features aside, it is just as important that AR glasses are optimized for efficient manufacturability and mass production. As a consumer product, it must be possible to manufacture AR smart glasses in high volumes and low enough cost.
This article will delve into what this means for the design and manufacture of AR glasses, specifically for the display system, and how TriLite addresses the challenges of mass manufacturability.
Meeting OEMs’ Expectations
We have previously described consumers’ expectation and their impact on the display specifications but there still exists another crucial set of expectations that must be met: the expectations of the OEMs, the companies that ultimately manufacture the AR glasses and bring them to market.
It goes without saying that OEMs are constantly looking for solutions that are mass-market-manufacturable and future-proof. So how does TriLite’s Laser Beam Scanning (LBS) technology stack up in this regard?
In order to address these expectations, TriLite has, from the very outset, implemented a ‘software-first’ approach, effectively and intentionally shifting complexity away from hardware into the software domain. Logically, reducing hardware complexity simplifies mass production, reducing component counts and critical failure/error points.
The company has built up a proprietary stack of algorithms (called the Trajectory Control Module, or TCM) for advanced control of the Trixel® 3 projector, thereby minimizing the overall size and complexity of the LBS optical system. Watch TriLite CEO, Dr. Peter Weigand, talk at SPIE 2023 about meeting OEM expectations.
In production, this ‘software-first’ approach enables substantial simplification of the LBS manufacturing process flow. Concurrently, it also increases assembly yield and loosens alignment tolerances for the placement of lasers, optical components (passive and active alignment), and the MEMS mirror, all of which have a beneficial impact on manufacturing costs.
Figure 1 is an example illustration of the power of the software-first approach – in a regular approach, significant effort may be expended on achieving optimal alignment of the three lasers. The TriLite system can co-exist with certain tolerances and fix errors by means of smart control of MEMS mirrors and lasers. Tolerance analysis has shown that manufacturing positioning tolerances are larger by a factor of three.
Figure 1: using software to achieve optimal laser alignment
Design for Manufacturing
The basic principles of Design for Manufacturing[1] typically include some or all of the following:
- Collaboration with experienced partners
- Using standard, common parts that can easily be obtained from multiple sources
- Simplifying product designs, including reducing the number of components
- Prototyping before mass production, to find and fix errors early and at a lower cost
How does TriLite meet these principles?
Firstly, it teams up with world-class companies to ensure high-quality, high-volume manufacturability. This includes names like TDK and Infineon for the MEMS mirror, RGB laser modules from ams OSRAM, and Dispelix for waveguides specifically optimized for use with the LBS.
TriLite chooses its partners based on their mass manufacturing capabilities. The ecosystem strategy focuses on partnering with world-class companies to ensure top-quality and reliable mass manufacturing.
In the production of the Trixel® 3 projector, the use of standard components and standard equipment is prioritized, and production flows are optimized for high volumes utilizing standard processes used for telecom and consumer devices.
For the purpose of prototyping, TriLite has engineering samples available for the Trixel® 3, which closely correspond to the final specifications for mass production. The micro PCB supplied for the driving electronics is already form factor, which helps customers to rapidly design and prototype their AR systems.
High Volume Adoption: LBS Versus microLEDs and Panel-Based Displays
The right choice of technology plays a critical role in high-volume adoption. There exist several technologies that are suitable for displays on AR glasses. These split into two main categories: scanning-based displays, such as Trixel® 3’s laser beam scanner (LBS), and panel-based display engines, which are like tiny computer screens. Panel-based display engines have recently seen wider adoption; however, they require external optics and are quite bulky. LBS display engines, on the other hand, can be both compact and bright.
MicroLED displays have enjoyed much publicity; however, in order to achieve high-volume adoption in the AR glasses space, they would first need to overcome several fundamental obstacles. Firstly, they exhibit inferior efficiency with small pixels, which consequently leads to lower brightness and increased power consumption, and associated thermal issues. To make matters worse, small microLED displays frequently suffer from poor yield and have difficulties in achieving uniform color and brightness characteristics.
LBS Advantages in Manufacturing: High Yield and Scalability
What about the use of microLED displays in mass manufacturing? For large displays with a large pixel pitch, such as TVs or automotive displays, microLEDs are a very viable solution. However, when used on AR glasses, microLEDs with small pixel pitches have yet to overcome some fundamental issues that are preventing mass adoption. Firstly, they have a lower efficiency when working with small pixels, which means a lower brightness, increased power consumption, and associated thermal issues.
Small microLED displays also suffer from poor manufacturing yield and difficulties in achieving satisfactory color and brightness uniformity. In contrast, LBS does not exhibit efficiency degradation when going to smaller pixel dimensions and, of course, there are no single-pixel failures on LBS systems.
According to Sam Dale, Senior Technology Analyst at IDTechEx, “Manufacturing at scale remains the most difficult problem to solve for microLED micro displays, with complex mass transfer processes and high defect rates being significant roadblocks.”[2]
It is paramount that the technology is scalable for future generations of AR glasses. Firstly, lower power laser sources and optical combiners with higher efficiency will become available as technology advances. In terms of achieving a better field of view and higher resolution, LBS technology in general (and Trixel products in particular) scales far better than panel-based displays and its size is the smallest in the industry. For panel-based displays, there are certain limitations to how small they can get. It generally applies that when resolution and field-of-view are increased, all panel-based systems tend to get larger, not smaller – which, again, gives a clear advantage to LBS in the area of scalability.
Conclusion
TriLite has set up its manufacturing services to meet its customers’ requirements for high-volume production. With a rapidly expanding ecosystem of manufacturing partners, TriLite designs for seamless mass production, incorporating customized standard components and utilizing state-of-the-art high-volume production equipment.
To enable customers to rapidly bring their products to market, TriLite has qualified a high-volume manufacturing services platform based around partnerships with key suppliers for assembly and components, for example, the MEMS mirror from Infineon and TDK.
In summary, the Trixel® 3 LBS meets both consumer expectations and OEM requirements. The technology is both scalable and future-proof, and the efficient ‘software-first’ design approach ensures it is suitable for mass production in high volumes and low cost.
[1]https://www.linkedin.com/advice/1/what-some-key-factors-consider-when-designing